Guide For Engineering Teams That Need A Production-Ready ECU
The ECU you choose can make or break your project.
Your ECU affects your development process, your costs, time to market, and your ability to scale for production. For these reasons the partner you choose to supply your ECU is very important. The right partner can go beyond just 'providing parts.' An ideal partner will look for ways to save you time, money, and empower you to Take Control of your project.
And while many engineering teams tend to think 'software first', your ECU choice will ultimately inform your choices for software and other tools. Not the other way around. With so much riding on your ECU (literally), it's important to understand basic selection criteria as well as the features and benefits of the products currently available. But first, a question...
Should You Build or Buy Your ECU?
This question is the first fork in the road for engineering teams when considering their ECU choices: Do I custom-build my ECU in-house or buy an off-the-shelf unit?
Here's a test:
Is this vehicle for personal use/Am I a hobbyist?
Will this vehicle be used for educational purposes? (Are you trying to learn electronics or trying to build something?)
Am I planning to make such a high volume of units that I am prepared to invest significantly upfront to cost-optimize down to small cost increments?
If you answered yes to any or all, you should consider a DIY approach.
Conversely, if you meet any or all of the following criteria, you should purchase your ECU:
Your goal is mass production
Rich Swortzel
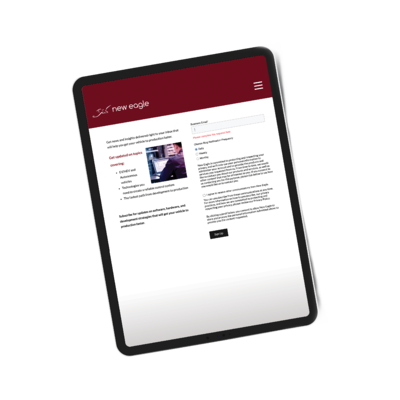
Stay up-to-date on what we're doing with Autonomous Mobility and electrification by subscribing to our specialized newsletters
How To Select An ECU For Your Autonomous or
Electric Vehicle Project
Most engineers find ECU selection one of the hardest parts of the development process. It can quickly get tricky to navigate the many options out there and to know what makes one ECU a better choice than another --or one supplier a better choice than another.
Below are six key areas of consideration for selecting the right ECU for your project and each of these areas is equally important for production vehicles.
1. Quality and Performance
Your vehicle or system (and its ECU) should be fully validated to meet industry safety standards and fully ruggedized to stand up to use in real life. Nothing is more damaging to your brand's reputation than a safety-related incident and/or quality failures and their subsequent recalls and warranty issues.
Large OEMs source their units from world-class suppliers such as Continental or BOSCH. Their units are validated by the most stringent performance standards in the industry. And they're proven in real life-- hundreds of thousands of vehicles on the road today are controlled by ECUs made by these manufacturers.
Look for an ECU production provider who has a robust supply chain that includes world-class manufacturers like BOSCH, Continental Automotive and Visteon. Their business is based on producing a high volume of quality ECUs and they can spread costs for quality, validation, plant and equipment across a very high unit output to keep per-unit costs down. They can provide a cost/capability/quality trade-off not found at typical low-volume ECU manufacturers. The difficultly is that these world-class suppliers have high system volume requirement minimums and/or require a significant upfront investment for development and tooling. Typically, there is significant lead time for these large, premier suppliers to produce an ECU and develop software specific to your custom application.
On the other hand, you can source controllers from small, local shops. There are software tool vendors who provide a solution to create custom software for ECUs produced by these boutique electronics fabrication shops. While these boutique-made ECUs may be well-engineered, it is difficult for them to be produced with the level of quality and validation that premier suppliers provide due to the fact that the plant and equipment, and processes would not be feasible if spread over a small number of units. In this case, economies of scale are not working in the favor of this type of solution.
2. Costs and Production
Sometimes the best-in-class ECU comes with a price tag that's out-of-reach. And sometimes a 'good deal' on an ECU isn't what it seems.
Look for an ECU supplier who can help you understand the differences between prototype pricing and pricing for production--and make sure that the supplier can scale with you as your business changes.
The sweet spot: A supplier who offers high-quality ECUs at volume pricing.
Look for automotive-born, production-grade ECUs. If you're scaling to production, look for an option to do your development on the production units. This will help you to avoid the cost and time to re-validate your application on different hardware.
3. Software and Processes With Production Capability
ISO 26262, the international standard for road vehicles that provides a framework for functional safety throughout the progression of electrical and electronic (E/E) systems development, is critical for teams with a vehicle heading to production.
While some requirements are product-specific, others focus on the safety regulations throughout the development lifecycle. These standards demonstrate how companies should integrate functional safety into their development process, providing regulations and recommendations on how to achieve appropriate functional safety measures. To put it simply, this is a common standard that assesses and verifies the safety of a system before it is put into service.
Select an ECU that supports software and development processes that are production capable and compatible such as the ISO 26262 standard.
Dwayne McKenzie
Your ECU supplier should have the engineering capabilities to help provide a clear path to production that incorporates the necessary safety standards that are required for today’s various industries. Ideally, they should be able to assist your company in clarifying whether the updated ISO 26262 standard applies to your project, conduct a risk assessment of your product and development cycle, provide you with functional safety capable hardware, and assist your team with how to incorporate their product into your system development and safety lifecycle.
4. IP Ownership and Maintenance
Josh Carroll
5. Supply Stability
Nothing is more frustrating than waiting on parts, or finding out that a part you need is out of stock or worse - out of production.
Always vet the longevity, efficiency, and stability of your ECU partner's supply chain. Can they guarantee that the part they sold you will be available for the duration of your vehicle's lifespan? This timeframe should include production and service parts.
Supplying electronics into the automotive supply chain requires continuity and guarantee of supply for 10+ years for production and aftermarket service.
"Look for an ECU production provider who carefully selects suppliers like the major OEMs, producers like BOSCH, Continental Automotive and Visteon, to provide mass quantities of reliable ECUs."
Kevin Alley
6. Service and Support
Your ECU supplier should understand the challenges of your unique project and offer ways to accelerate time-to-market and set you up for continued success. Ask your prospective suppliers about application templates, engineering resources, onboarding for new engineering team members, and continuous training for everyone.
Also, ask them:
- What happens when there's a problem?
- How can we get a hold of you?
- Who can we call?
- How quick are your response times?
ECUs are highly-engineered products. You'll need the dedicated support of the people who built them throughout your project and long afterward.
20 Questions To Ask A Potential ECU Supplier
- Can you deliver validated, automotive-born units that are on par with world-class manufacturing industry standards? (ISO 9000 / ISO 9001)
- What type of environments can your product operate in?
- Do you provide ruggedized, validated units?
- Is the pricing economical at volume?
- How many units can you produce?
- Can you meet our project timing?
- What is the lead time needed for your ECU?
- Can you meet our safety requirements? (ISO 26262)
- Can you scale with our business needs?
- Who will have control over our IP?
- Can we make minor tweaks to the functionality on our own, or will we need to re-engage with you for help?
- What is your turn-around time for repairs/replacement help?
- Is your business stable/do you have a stable supply chain?
- Do you have templates, intellectual property and training to help our team get started quickly?
- What can you offer us beyond the ECU? (do they have a toolchain?)
- Will we have access to engineering and product support?
- Will the people who built my ECU be the same people supporting it?
- How accessible will you be for troubleshooting/repairs/replacement?
- Will we be assigned to a specific point-of-contact that we can call for quick help?
- Can you supply testimonials or proof of success from working organizations/projects similar to yours?
Developing Control Systems Faster With Raptor
Learn how Raptor helps you take control of your vehicle development process from concept to production.